Nonswirl Nozzlles
Nonswirl Nozzlles
Technical characteristics
In 1986 – 1987 VIO in collaboration with Borovichi Refractories Plant has developed process of corundum-graphite nonswirl nozzles production, which excluded application of unavailable and expensive materials – crystalline silicon and silicon carbide and use of expansive operations of hard firing and air brick glazing.
During 1986 – 1990 corundum-graphite nonswirl nozzles of KG grade have been tested and found application at all largest metallurgical plants in USSR: CherMK, NLMK, OKhMK, OEMK, UzbMZ, BMZ. Corundum-graphite nonswirl nozzles exhibited at VDNKh in USSR and awarded silver medal in 1989. It is known that corundum-graphite nonswirl nozzles the same as submersible nozzles are apt to healing, especially during teeming of aluminum-killed steels. Healing of nozzle channel is conditioned by number of physico-chemical processes. Healing leads to loss of efficiency of continuous-casting plants, necessity of blowing of “healed” nozzle channel by oxygen gas, early termination of teeming and finally to stock appreciation.
Further developments of JSC “Borovichi Refractories Plant” on advancement of production processes resistant to healing of nonswirl nozzles, lead to creation of biceramic product with so called “anticlogging” coating of nozzle channel, which prevents its healing by nonmetallic deposits. Well-known fact of absence of healing in nonswirl nozzles based on zircon push to the following in-house development this time – zircon-based anticlogging coating. Nonswirl nozzle with zircon-based coating did not displayed surface deterioration of working channel or any deposits after service.
JSC “Borovichi Refractories Plant” has developed production process of nonswirl nozzle with porous insert inside channel for argon blow, which considerably decreased extent of steel-pouring channel healing by nonmetallic inclusions.
Rate for grade | ||||
---|---|---|---|---|
Nonswirl nozzles | Collector nozzles | |||
KUSD-80 | КUSD-GS |
МКUSТ-80 | ||
Main layer | Gas-permeable layer | |||
GOST R 52801-2007 | Spec. 14-194-299-10 | GOST R 52707-2007 rev.1 | ||
Mass fraction, %: |
|
|||
Al2O3 (of baked substance), minimum | 80 | 80 | 80 | 80 |
С, withing limits of | 5-9 | - | - | 5-8 |
С (Changes in weight during baking) | - | 5-9 | minimum 4 | - |
Compressive strength, N/mm², minimum | - | 30 | 20 | - |
Open porosity, %, maximum | 13 | 13 | 18 | 12 |
Rate for grade | ||
---|---|---|
КGI | SDPU | |
Spec. 14-194-230-98 | Spec. 14-194-284-08 | |
Mass fraction of baked substance, %: Al2O3, minimum MgO, minimum С, withing limits of |
- 5-9 |
90 8-11 |
Apparent density, g/cm³, minimum | - | 2,87 |
Open porosity, %, maximum | 13 | 8 |
KGI – graphitiferous nonswirl nozzle
SDPU – periclase-carbonaceous nonswirl nozzle
Rate for grade | |||||||
---|---|---|---|---|---|---|---|
SD-KG | SD-КGV |
SD-КG1V1 | SD-KG1V2 | ||||
Spec. 14-194-283-08 | |||||||
|
|
product shank | funnel | product shank | funnel | product shank | funnel |
Mass fraction of dry substance, %: Al2O3, minimum С, minimum MgO, minimum |
67 13 - |
45 26 - |
67 13 - |
45 26 - |
- 13 70 |
45 26 - |
- 10 65 |
Apparent density, g/cm³, minimum | 2,60 | 2,28 | 2,60 | 2,28 | 2,60 | 2,28 | 2,50 |
Open porosity, %, maximum | 20 |
Rate for grade | ||||||
---|---|---|---|---|---|---|
SD-КG2V | SD-КG2V1 | SD-КG2V2 | ||||
Spec. 14-194-283-08 | ||||||
|
product shank | funnel | product shank | funnel | product shank | funnel |
Mass fraction of dry substance, %: Al2O3, minimum С, minimum MgO, minimum |
47 23 - |
67 13 - |
47 23 - |
- 13 70 |
47 23 - |
- 10 65 |
Apparent density, g/cm³, minimum | 2,40 | 2,60 | 2,40 | 2,60 | 2,40 | 2,50 |
Open porosity, %, maximum | 20 |
Shape and dimensions of nonswirl nozzles should correspond to the customer’s drawings, approved by the manufacturer. Working surface is specified in the drawings.
Nonswirl Nozzles of fast change
Rate for grade | |||
---|---|---|---|
BSDKG2V3 | |||
Technical agreement | |||
|
Main composition | Gas-permeable layer | Contact surface |
Mass fraction of dry substance, %: Al2O3, minimum С, minimum |
47 23 |
55 9 |
53 9 |
Apparent density, g/cm³, minimum | 2,40 | 2,45 | 2,40 |
Open porosity, %, maximum |
20 |
25 | 20 |
Form an ddimensions GOST R 52801-2007
Number | Dimensions, mm | ||||||||||
---|---|---|---|---|---|---|---|---|---|---|---|
H | h | D | D1 | D2 | d | d1 | r | e | k | h1 | |
9 | 290 | 20 | 160 | 116 | 136 | 50 | 40 | 70 | 68 | 90 | - |
10 | 52 | 42 | 68 | 90 | |||||||
11 | 56 | 46 | 68 | 90 | |||||||
12 | 60 | 50 | 67 | 95 | |||||||
13 | 66 | 56 | 66 | 99 | 3 | ||||||
14 | 70 | 60 | 65 | 101 | |||||||
15 | 290 | 25 | 190 | 130 | 160 | 65 | 55 | 70 | 68 | 97 | - |
16 | 70 | 60 | 66 | 100 | |||||||
17 | 75 | 65 | 65 | 103 | 3 | ||||||
18 | 80 | 70 | 65 | 104 | - | ||||||
19 | 85 | 75 | 65 | 110 | 5 | ||||||
20 | 90 | 80 | 65 | 112.5 | |||||||
21 | 100 | 90 | 63.5 | 117.5 | |||||||
22 | 290 | 20 | 160 | 116 | 136 |
20 22 24 26 28 30 32 34 36 38 40 42 44 46 48 50 52 54 |
43 | 52 | 40 | 115 | 16 |
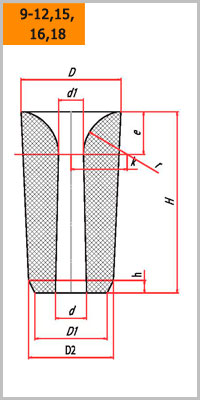
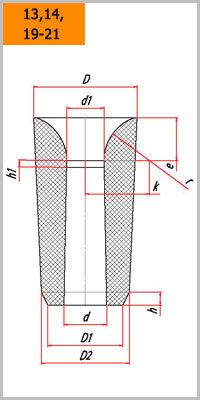
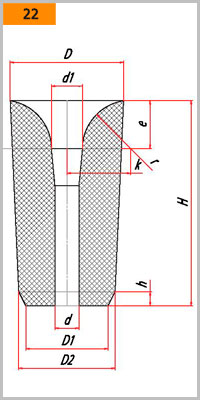
Limit deviations of dimensions
Dimensions, mm | Limit deviations, mm |
---|---|
Diameter: | |
up to 50 inc. | ±1 |
over 50 up to 100 inc. | ±2 |
over 100 | ±3 |
Height | ±10 |
Height of bead and grooves | ±1 |